Annealing Furnace
Annealing Gold, Silver, and Platinum In Jewelry Making
SuperbMelt annealing furnace is designed for annealing precious metal, such as gold, silver, and platinum in jewelry making. It works by the precious metal part is heated above the recrystallization temperature and then cooled after the material has been held at the desired temperature for a period of time.
The annealing process can improve the workability, mechanical properties and electrical properties of the workpiece metal. It goes through 3 stages, which are; the recovery , recrystallization and the grain growth stage.
The maximum power required for the metal annealing furnace is only 9kw, while the ammonia decomposition power is only 5kw. The machine adopts an intelligent PID temperature control device, which can work 24 hours and has an alarm function, effectively ensuring the safety and efficiency of the metal annealing process.
- Annealing furnaces are used to change the work hardening phenomenon in metal processing such as curving, rollingor When the hardness of the metal material is too high, it cannot be processed or even cracked. Therefore, the annealing furnace is needed to stabilize the working process.
- Using annealing equipment to heat a metal workpiece to a temperature above recrystallization, the metal in this state is malleable for reprocessing.
- It relieves stress that may occur when the metal workpiece solidifies.
- It is suitable for heat treatment of all kinds of precious metal jewelry on the market, such as pure gold, 18k gold, pure silver, 925 silver, brass, white copper, red copper, hardware, alloy stamping parts, etc.
- The whole process of annealing is protected by ammonia gas, which ensures that the metal surface will not be oxidized and discolored, and there is no loss, which meets the processing standards of the jewelry industry.
- Ensuressafely on all annealing furnaces. Which is why the annealing furnace is equipped with a rod that feeds the workpiece into the high temperature section. The rod can easily be pushed and flipped at 180 degree celsius to drop the workpiece into the water chamber.
- The annealing process is controlled and monitored through the ammonia decomposition switch, alarm and timing switch configured on the machine.
- Equipped with a high-performance ammonia decomposition hydrogen system, PID intelligent control, simple operation, and timing switch.
- The maximum temperature required by the equipmentis 9kw at 1100 degree celsius.
- Metal workpieces are heated within 40 to 60 minutes, this contributes to a fast and efficient annealing process during production.
- Reducesthe original brittleness of the metal and enhance its electrical conductivity and magnetic properties.
- The collecting basket and water tank are used to collect work pieces and for immediate cooling of workpieces respectively.
- The ammonia tube locking interface prevents gas leakage after transportation.
- The entire dimension and weight of the annealing furnace for sale are 850*1400*1600mm (W*L*H mm) and 135kg respectively.
Model number | SPB-AWF2 |
Power source | 3 phase 380V, 50/60Hz |
Power | 9kw |
Ammonia decomposition Power | 5kw |
Heating time | 40-60 minutes |
Max. temperature | 1100℃ |
Used gas | Ammonia gas |
Working slot width | 200*100*750 (W*L*H mm) |
Dimension | 850*1400*1600mm (W*L*H mm) |
Weight | 135kg |
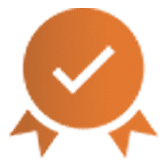
2 years warranty
The warranty for our machine is one year longer than the warranty provided by other factories.
Strong service team
We will give response within 24 hours against your problem by our professional engineer.
Why SuperbMelt Annealing Furnace
Any Question About SuperbMelt Annealing Furnace
Guide of Annealing Gold, Silver, and Platinum In Jewelry Making
What Is Precious Metals Annealing?
Annealing is said to be a treatment process focused on altering the physical and or the chemical properties of a given material. This alteration is intended to enhance ductility while reducing the hardness of the material so that it is easily workable.
For the annealing process to work efficiently, the material must go above its recrystallization temperature for a given duration before being allowed to cool. The cooling rate varies based on the nature of the metal being annealed.
This annealing method is suitable for precious metal jewelry manufacturing industries such as pure gold, silver, copper, K gold, copper alloy, 925 silver, etc.
What Is Work Hardening When Annealing Precious Metals?
Work hardening, also known as cold hardening, refers to the situation that when plastic deformation occurs below the crystallization temperature, the strength and hardness will increase, while the plasticity and toughness will decrease.
The occurrence of work hardening makes it difficult to reprocess metal workpieces. For example, when minting gold coins, gold bars, it will be too hard to press out a complete pattern. The effect of the design of bangles and beads will be very poor. Gold chains weaving also could not be completed.
The annealing process is to improve the phenomenon of work hardening through heat treatment. The metal is heated to a certain extent and cooled at a suitable temperature, which reduces the hardness and makes the metal workpiece soft and bendable, so that the rolling sheet, wire drawing, and chain making process can be done easily.
How to Anneal Precious Metals?
Metals are oxidized during annealing heat treatment, so annealing must continue in the process of oxidation until the metal turns red. It should be noted that when the metal turns dark red, the critical temperature is reached, and the heating needs to be stopped immediately. Otherwise the metal may be melted.
Then followed by quenching, which means that the heat-treated metal is cooled in water to the extent that it can be reworked. A piece of metal can be annealed multiple times, and the degree of annealing is controlled as long as it can ensure that the metal will not become very hard during the reprocessing process, can support the modeling operation and will not dry out.
It is easier to master the annealing technique through experience. If you are a newcomer, we will also provide some detailed data for your reference.
3.1, How To Anneal Gold?
For gold of different purity and form, the annealing time and temperature are different. For gold of different shapes, we also need to use the correct method to deal with it.
- Yellow and White Gold Alloys
The degree of annealing of gold alloy is basically heat treatment at 676℃ for 10 minutes to light red, and then water quenching.
Platinum alloys need to be heated at 732℃ for 10 minutes to dark orange before water quenching.
- Thick and Thin Lines
Both gold thick and thin wires should pay attention to the adjustment of temperature and time. The temperature must be lower than the melting point of gold. When heating, turn the workpiece to make it evenly heated. After turning red, put it in water to quench. For thin wire annealing, when winding the coil, pay attention to plugging the two ends to fix the whole coil to prevent it from spreading out during heating.
- Sheets and Blocks
For gold sheet and bar, we developed a special tunnel furnace, which is more suitable for manufacturers with mass production needs, and it has a welding function. When the welding auxiliary material is placed between two metals, it can help the two workpieces are connected in the heating process. and the annealing process realizes welding at the same time, which makes the work more efficient.
3.2, How To Anneal Silver?
Even without annealing, since the hardness of silver itself is not very high, it can reach 70% cold working.If sterling silver is annealed, it needs to be heated to 593°C to turn dull red, then quenched in water.
It should be noted that the annealing of pure silver needs to be done in conjunction with protective non-oxidizing materials. After the annealing is completed, put the silver workpiece into the pickling solution for a few minutes to remove the protective material.
3.3, How To Anneal Platinum?
The annealing temperature of platinum needs to reach 982°C. After it turns bright orange, the platinum workpiece can be cooled naturally or in water. Due to the nature of platinum, 70% cold work can be achieved before annealing.
For the annealing of platinum alloys, such as 950Pd and 950Pt, it can be heated at 982°C for about 15 minutes then quenched.
3.4, Common Problems Encountered in Precious Metal Annealing?
When should precious metals be annealed?
- When your next step involves drawing the metal into wires, rolling sheets, etc. that need to change the material, annealing will facilitate the forming of the metal, and there will be no problem of dry cracking.
- If the metal needs to be bent and forged. Annealing softens the metal and makes it easier to shape.
How to adjust the flame size of annealing?
The flame usually needs to be large and soft. When annealing precious metals with good thermal conductivity, increase the flame according to the size of the workpiece, so that the heating will be more sufficient.
Why Choose SuperbMelt Annealing Furnace
SuperbMelt is your number one stop for all your annealing needs. Note that besides providing some of the best annealing furnaces, we can help you with the work on-site.
Better still, if you choose to purchase any of our products, we will supply you with a comprehensive manual to enhance your experience. At the time of writing this guide, from us, you can get an annealing furnace that comes in a compact design, with a range of features that you will find useful.
Before we delve deeper into this section, it is vital to understand that SuperbMelt has a wide range of annealing surfaces. We will mention some of have mentioned them in the next section of this chapter.
4.1, Types of SuperbMelt Annealing Furnaces
We have annealing furnace and mesh belt furnace. Both of them are all designed for professional precious metals.
Their application is easy, but we will be there for you every step of the way to see that you have the best user experience with our products.
The SuperbMelt annealing furnace is creatively designed to heat metals above recrystallization temperature. Once the desired temperature has been achieved and maintained for some time, the furnace will cool back the metal so that the necessary results are achieved.The entire annealing process is carried out under the protection of ammonia gas, so that the workpiece will not be oxidized and retain the original color.
With our furnace, you will enjoy enhanced machinability and electrical and mechanical properties of your workpiece metals.
For instance, with a maximum power of 9kw, with ammonia decomposition of around 5kw, you will achieve a lot.
4.2, What is the Working Principle of SuperbMelt Annealing Furnace?
SuperbMelt annealing furnaces use electric power to heat workpieces to the desired temperature and cool them back. Without consuming too much power, the furnaces leverage unique features to ensure that the working surfaces don’t get oxidized.
After the entire process is completed, you will end up with a ductile workpiece that can be used for a range of applications without developing internal stress. The entire process doesn’t take too long, so within a day, you can get a lot of work done without sacrificing quality.
Recrystallization is a process that is accompanied by the reduction in hardness and strength of the material while ensuring a significant increase in ductility
4.3, Technical Specification Difference of SuperbMelt Annealing Furnaces
For a clear presentation of this crucial information, we have shared the specs of the two machine separately. Let us begin with the Annealing Furnace:
- Model number-SPB-TF
- Power-9kw
- Ammonia decomposition power-5kw
- Heating time-40-60 minutes
- Maximum temperature-1100 degrees centigrade
- Used gas-ammonia
- Working slot width -850*1400*1600mm (W*L*H mm)
- Weight-135kg
Below are the specs for the Mesh Belt Furnace:
- Model number-SPB-AWF
- Power source-3 phase 380V, 50/60Hz
- Power-13kw
- Maximum temperature-950 degrees centigrade
- Speed-sleepless speed regulation
- Cooling way-water cooling
- Used gas-Ammonia
- Working slot-70*40 (W*L mm)
- Network bandwidth-50mm
- Dimension-3000*600*1500 (W*L*H mm)
4.4, What are The Advantages of SuperbMelt Annealing Furnace
Unlike the other furnace, our mesh belt furnace is divided into two integral parts. The left side contains the furnace chamber ammonia flowmeter, while the right chamber contains the cooling water ammonia flowmeter.
To run this furnace, you will need to supply it with a maximum power of 13kw and a maximum temperature of 950 degrees centigrade. This furnace is specifically designed for the hardware industry, more so for the jewelry-making companies.
It is also made for the coin bar minting industry. It can be used on silver, k-gold, and cast iron workpieces. This explains why it comes with a wide range of features and uses slightly high electric energy.
The combined frame of the furnace is not hard to install and can also be dismantled in seconds. The features are also well designed so that they can stand some rough handling.
Your furnace will come with some purification device of nitrogen that is produced through ammonia decomposition. SuperbMelt is an annealing furnace manufacturer, and our products come with a temperature regulator, timing setter, cooling chamber linear regulator.
The furnace also leverages a speed regulator for the mesh belt. This ensures excellent perfect control and efficiency in the workplace. With the timing setter control, you can schedule automatic annealing, which means you will have some time to focus on other important things.
About the Annealing Furnace FAQ
- 1. How does an annealing furnace work?
- 2. What furnace is used for annealing?
- 3. What is annealing and why is it used?
- 4. What is the temperature of the annealing furnace?
- 5. Does annealing increase hardness
- 6. How does an annealer work
- 7. How to anneal metal
- 8. What does annealing do to metal
- 9. What temperature is annealing done at
1. How does an annealing furnace work?
Annealing furnaces work by heating a metallic material to a specific temperature and then gradually cooling it. There are several key steps in this process:
- Heating: The material is placed in the furnace and the temperature is raised above its recrystallization temperature or below its melting point. This temperature varies depending on the material and its properties.
- Immersion: Once the desired temperature is reached, the material is held at that temperature for a predetermined period of time. This allows the internal structure of the material to become more homogeneous and relieves internal stresses.
- Cooling: After the soaking period, the material is gradually cooled at a controlled rate. This is done by switching off the heating elements or by introducing a cooling medium such as air or water into the furnace.
- Protection: In some cases, the annealing process is carried out under a protective atmosphere such as hydrogen or ammonia. This prevents oxidation and preserves the surface properties of the material.
- Recrystallization: During the heating and soaking stages, the internal structure of the material undergoes recrystallization. This process results in the formation of new, smaller, more uniformly distributed grains, which reduces hardness and increases ductility.
The purpose of annealing is to improve the machinability of the material, reduce internal stresses and increase its mechanical properties. Different materials require specific annealing temperatures, soaking times and cooling rates to achieve the desired results.
2. What furnace is used for annealing?
Annealing furnaces are used for the process of annealing, where a material is heated to a specific temperature and then gradually cooled to change its properties. There are several types of furnaces that can be used for annealing, each designed to accommodate different materials and applications. Some common types of annealing furnaces:
- Chamber Furnaces: these are versatile furnaces with a box-like structure that can be heated to high temperatures. It is commonly used for annealing metals, ceramics and glass.
- Tube Furnace: A tube furnace is cylindrical in shape and provides a controlled annealing environment. It is suitable for applications requiring uniform heating, such as processing small samples or fragile materials.
- Continuous Furnaces: Continuous furnaces are used for mass production and have conveyor systems that move material through a series of heating and cooling zones. They can process large quantities of material efficiently.
- Bell-type furnaces: These furnaces have a bell-shaped chamber that can be lowered over the material to create a controlled atmosphere during the annealing process. They are commonly used for heat treatment of metals.
- Mesh Belt Furnaces: Mesh belt furnaces are used for continuous annealing processes and are particularly suitable for products such as wire, strip and tube. The material is placed on a mesh belt, which moves through the furnace to achieve continuous heating and cooling.
- Vacuum Furnaces: Vacuum furnaces produce a controlled atmosphere by removing air and gases from the furnace chamber. Vacuum furnaces are used for oxygen-sensitive annealing applications or applications requiring a clean environment.
The choice of furnace depends on factors such as the type of material to be annealed, the desired properties, the size of the production and the specific requirements of the process. Different furnaces offer different degrees of temperature control, atmosphere control and heating rates to achieve the desired annealing results.
3. What is annealing and why is it used?
Annealing is a heat treatment process used to change the physical and sometimes chemical properties of a metal or alloy. Annealing is the process of heating a material to a specific temperature and then slowly cooling it to make the desired changes in its microstructure and properties.
The main purposes of annealing are:
- Relief of internal stresses: Internal stresses occur during the manufacture or processing of materials due to factors such as plastic deformation, cold working or rapid cooling. Annealing helps relieve these stresses and reduces the risk of material distortion, cracking or failure.
- Increased Ductility: Annealing increases the ductility of a material by rearranging the lattice, reducing dislocations, and increasing the deformability of the material. This is critical for materials that need to be shaped or molded.
- Reduced Hardness: Cold working or mechanical deformation can increase the hardness of a material. Annealing softens the material through recrystallization, which reduces hardness and improves workability.
- Refinement of microstructure: Annealing helps to refine the microstructure of a material, thereby improving mechanical properties such as toughness, fatigue and creep resistance.
- Improve machinability: Annealing reduces the hardness and increases the ductility of the material, which improves cutting and molding processes and makes the material easier to machine.
- Improve electrical and thermal conductivity: annealing can make the grain structure more uniform and refined, thereby improving the electrical and thermal conductivity of the material.
- Annealing is commonly used in industries such as metallurgy, manufacturing, aerospace and electronics. Annealing is used for a variety of purposes, including shaping the metal, improving casting properties, reducing brittleness, and preparing the material for subsequent processing steps.
There are several types of annealing processes, including complete annealing, process annealing, stress relief annealing and recrystallization annealing. The specific choice of annealing method depends on factors such as the type of material, initial condition, desired properties and intended application.
4. What is the temperature of the annealing furnace?
The temperature of an annealing furnace can vary widely depending on the material being annealed and the specific objectives of the annealing process. Different materials have different recrystallization temperatures, which is the temperature at which the material’s microstructure starts to change and internal stresses are relieved.
For example:
- Steel: The annealing temperature for steel is typically around 600°C to 900°C (1112°F to 1652°F) depending on the type of steel and the desired properties.
- Copper: The annealing temperature for copper is around 400°C to 700°C (752°F to 1292°F).
- Aluminum: The annealing temperature for aluminum is around 250°C to 350°C (482°F to 662°F).
Precious metals like gold, silver, and platinum also have specific annealing temperature ranges, typically falling between 600°C to 1000°C (1112°F to 1832°F) depending on the alloy and desired outcomes.
It’s important to note that the annealing temperature is usually below the melting point of the material to avoid melting. The material is heated to the annealing temperature and held there for a specific period of time, allowing internal stresses to relax and recrystallization to occur. Afterward, the material is slowly cooled to room temperature or another specified cooling rate.
The annealing process requires precise control of temperature and time to achieve the desired material properties. Different types of annealing (full annealing, stress relief annealing, etc.) may have slightly different temperature ranges and time durations.
5. Does annealing increase hardness
No, annealing decreases hardness rather than increasing it. In the heat treatment procedure of annealing, a material is heated to a specified temperature and then progressively cooled. The main goal of annealing is to soften and increase the ductility of a material by reducing its hardness.
The material’s internal tensions are reduced and its microstructure is altered during annealing. A decrease in hardness results from the process, which enables the atoms of the substance to move and arrange themselves in a more regular manner. This is especially advantageous for materials that have gone through cold working procedures like rolling or drawing, which can make them harder and less ductile.
The material becomes more pliable and practical to work with after annealing. It acquires better flexibility, formability, and machinability as well. As a result, additional heat treatment procedures like quenching and tempering, which require controlled cooling to achieve particular hardness levels, are utilised if the goal is to improve hardness.
6. How does an annealer work
Annealing furnaces, also known as annealing ovens, are specialized equipment used to anneal a variety of materials. The basic working principle of an annealing furnace is to achieve specific material properties by controlling the heating and cooling cycles. Here is how an annealing furnace works:
- Heating
- Immersion
- Cooling
- Protective atmosphere
- Cooling stage
The annealing process is effective in changing the microstructure of the material, removing stresses, improving ductility and increasing mechanical properties. The metalworking industry typically uses annealing after cold working processes such as rolling or drawing to soften the metal and prepare it for further processing.
7. How to anneal metal
Annealing metal involves carefully heating and cooling it in a controlled manner to achieve desired material properties. Here’s a general guide on how to anneal metal:
- Preparation:
Clean the metal surface to remove any contaminants that could affect the annealing process.
Identify the type of metal you’re working with and research its recommended annealing temperature and time.
- Heating:
Place the metal in a suitable annealing container or annealing furnace.
Heat the metal slowly to the recommended annealing temperature. The heating rate should be gradual to prevent thermal shock.
- Soaking:
Once the metal reaches the annealing temperature, maintain it at that temperature for a specific period of time. This allows for the internal stresses to relax and the microstructure to homogenize.
- Cooling:
After the soaking period, begin the cooling process. The cooling rate should also be slow to avoid introducing new stresses or warping the metal.
Some materials may require controlled cooling in a furnace, while others can be air-cooled.
- Protective Atmosphere (if needed):
Depending on the material, you might need to anneal it in a protective atmosphere to prevent oxidation. This is common for metals like steel and copper.
- Monitoring:
Keep an eye on the color of the metal as it heats up. Once it reaches the desired annealing temperature, it will change color due to oxidation.
- Final Steps:
Once the metal is fully cooled, remove it from the annealing furnace or container.
If necessary, clean the metal to remove any oxidation or scale that formed during the process.
- Testing:
Perform hardness or other material property tests to ensure the desired changes have occurred in the metal’s microstructure.
It’s important to note that the annealing process can vary depending on the type of metal you’re working with. Different metals have different annealing temperatures and cooling requirements. Always refer to the specific guidelines for the metal you’re working with and consider factors such as heating method, protective atmosphere, and cooling rate. If you’re new to annealing, it’s recommended to start with small test pieces to understand how the process works for your specific material.
8. What does annealing do to metal
Annealing is a heat treatment process that has significant effects on the properties of metal. When metal undergoes annealing, it goes through changes in its microstructure, which in turn affects its mechanical, physical, and sometimes even chemical properties. Here’s what annealing does to metal:
- Reduced Hardness: Annealing softens the metal by reducing its hardness. This is achieved by allowing the metal’s crystalline structure to become more uniform and relaxed, leading to improved ductility and decreased brittleness.
- Relief of Internal Stresses: During the fabrication and processing of metals, internal stresses can accumulate. Annealing helps to relieve these stresses by promoting the reordering of atoms and the reduction of dislocations within the crystal lattice.
- Grain Growth and Recrystallization: The heat during annealing encourages the growth of larger and more uniform grains in the metal’s microstructure. This process, known as recrystallization, results in improved material homogeneity and reduces the chances of defects and impurities.
- Improved Machinability: Annealed metal is easier to work with. It can be machined, formed, bent, and manipulated with less effort and reduced risk of cracking or failure.
- Enhanced Ductility: Ductility refers to the ability of a metal to deform without breaking. Annealing increases ductility, making the metal more pliable and capable of enduring shaping processes.
- Reduced Brittleness: Annealing reduces the likelihood of the metal becoming brittle or prone to cracking when subjected to stress or impact.
- Improved Electrical and Thermal Conductivity: Annealed metal usually has higher electrical and thermal conductivity due to its improved crystal structure.
- Homogenization of Alloy Composition: For alloys, annealing helps to homogenize the distribution of alloying elements within the material, creating a more consistent composition.
- Residual Stress Reduction: Annealing can reduce or eliminate residual stresses that accumulate during manufacturing or forming processes, leading to more stable and predictable behavior of the metal.
- Enhanced Grain Boundary Properties: Annealing can improve the properties of grain boundaries, such as resistance to corrosion and susceptibility to crack propagation.
In summary, annealing plays a crucial role in optimizing the properties of metal to suit specific applications. It can make metals easier to work with, improve their mechanical properties, and ensure their reliability in various environments and conditions.
9. What temperature is annealing done at
The temperature at which annealing is done depends on the type of material being annealed and the desired outcome. Annealing temperatures typically fall within a specific range, and the specific temperature chosen is influenced by factors such as the material’s composition, its initial condition, and the intended properties after annealing.
For different types of materials commonly annealed:
Steel and Iron: Annealing steel and iron is usually done between 600°C to 950°C (1112°F to 1742°F). The specific temperature within this range depends on the type of steel and the desired results. Lower temperatures produce a softer material, while higher temperatures promote grain growth.
Copper and Copper Alloys: Copper and its alloys are often annealed around 400°C to 700°C (752°F to 1292°F), depending on the alloy and application.
Aluminum and Aluminum Alloys: Aluminum and its alloys are typically annealed between 150°C to 350°C (302°F to 662°F). Higher temperatures can lead to over-aging or recrystallization.
Brass and Bronze: Annealing temperatures for brass and bronze fall within the range of 300°C to 650°C (572°F to 1202°F), depending on the alloy.
Stainless Steel: Stainless steel can be annealed between 700°C to 1200°C (1292°F to 2192°F), depending on the grade and properties desired.
Silver: For precious metals like silver, annealing is often done around 600°C to 700°C (1112°F to 1292°F).
It’s important to note that while these temperature ranges are common, precise annealing procedures can vary based on the specific alloy, intended properties, and the desired balance between softening the material and controlling grain growth. It’s recommended to refer to material-specific guidelines or consult with metallurgical experts for accurate temperature recommendations for annealing particular materials.