Mini Gold Melting Furnace
The Most Popular SuperbMelt 1-2kg mini gold (Ag, Cu, Al etc) melting furnace on the market
SuperbMelt mini gold melting furnace (SPB-DH) is suitable for any of your small-scale gold production. It is capable of melting any gold piece whose weight fall in the range 1-2Kg.
This small gold smelting machine can in no time reach a maximum temperature of 1600℃. This features also makes this machine for melting other metals. Metals such as silver, copper and aluminum, just to mention a few.
SuperbMelt mini gold melting furnace also finds application in jewellery recycling. It also very suitable for gold diggers in deals in collecting gold and its alloys.
If you wanna check gold melting furnaces with bigger capacity, Please click here.
Model number | SPB-DH1 | SPB-DH2 |
Power source | Single phase 220V, 50/60Hz | Single phase 220V, 50/60Hz |
Power | 3.5 kw | 3.8 kw |
Applicable metal | Gold, Silver, Copper, Brass, Bronze, and their alloys | Gold, Silver, Copper, Brass, Bronze, and their alloys |
Melting time | 2 minutes | 2 minutes |
Max capacity | 24K Gold: 1.2 kg 18K Gold: 1.0 kg 925 Silver: 0.6 kg | 24K Gold: 2.4 kg 18K Gold: 2.0 kg 925Silver: 1.2 kg |
Max temperature | 1600℃ | 1600℃ |
Temperature control k-type | Optional | Optional |
Dimension | 520*400*330mm | 520*400*330mm |
Weight | 21 kg | 22 kg |
Heating technology | Induction heating | Induction heating |
Cooling way | Water cooling | Water cooling |
- The mini gold melting furnace takes a minimum of two minutes to melt a batch of two kilograms of any precious metal. This sums up to producing approximately 30kg of gold in an hour.
- Also, this electric gold melting furnace can work for 24 hour none stop. At the same providing you with excellent services and efficient gold melting process.
- SuperbMelt electric small smelting furnace uses the latest IGBT induction technology. This technology reduces your power consumption and improves your production efficiency. This mini gold melting machine speeds up your melting processes. This serves as its competitive over any other furnace in the market.
- It comes with video tutorials and installation guide. This makes installation on other operations very simple and easy to go about.
- SuperbMelt mini gold melting equipment is environment-friendly. It comes with the latest inbuilt green technology which is now being employed in the gold industry. It does not produce harmful gas and fumes which are associated with other gold melting furnaces.
- This mini furnace is designed very simple and easy to use. Compact and small-sized as compared with other furnaces that takes a lot of space
Graphite crucible for gold/Silver melting Furnace
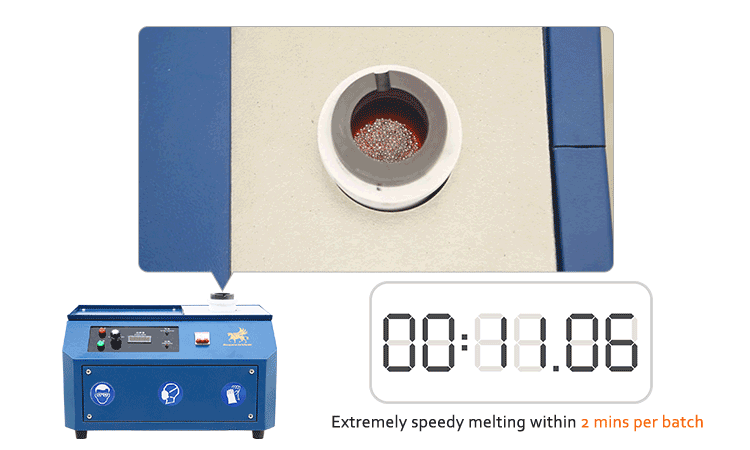
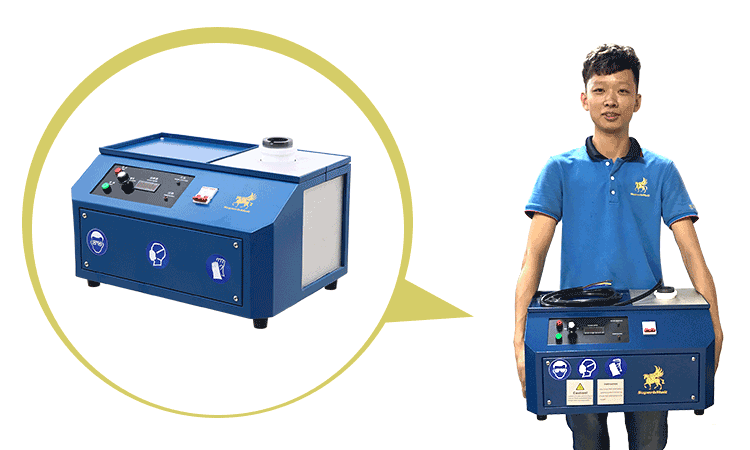
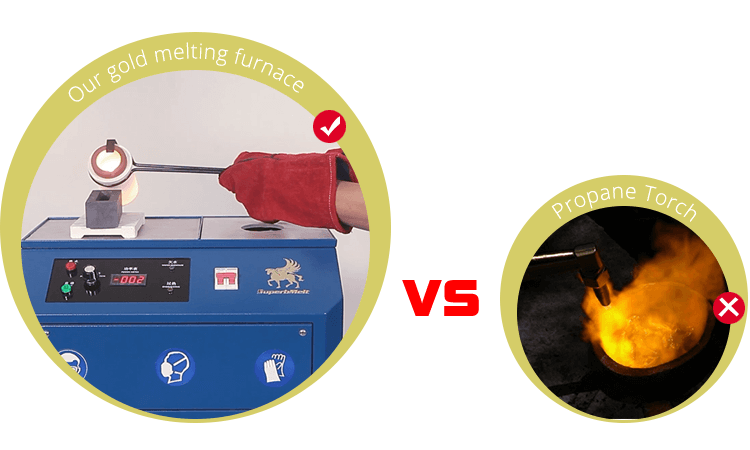
Why SuperbMelt 1-2kg Mini Gold Melting Furnace
Helpful Resource For Your Reference ( An expert about SuperbMelt mini gold melting furnace )
3-6kg gold smelting pot kit
More Gold Melting and Casting Machinery For Your Choice
Any Question About SuperbMelt Mini Gold Melting Furnace
FAQ Guide of Gold Melting Machine
- Why do you need an induction melting furnace?
- How does an induction melting furnace work?
- How to melt different kinds of metals?
- How to choose the induction melting furnace you need?
- How efficient is induction heating?
- What temperature can the induction melting furnace reach?
- What can I use as a crucible?
- What is the difference between an electric arc furnace and induction furnace?
- What is the difference between smelting and melting?
- How do you smelt gold with borax?
- How do you separate gold from other metals by melting?
- How do you melt gold jewelry?
- How do you get gold from gold ore?
- How do you get impurities out of gold?
- How can I reduce the power consumption of my induction furnace?
- What is the difference between an electric arc furnace and induction furnace?
- Does induction use less electricity?
- At what heat (temperature) does gold melt?
- What flux do you use to smelt gold?
- How much borax is required to melt gold?
- What is the process of smelting gold?
- Can you smelt gold in cast iron?
- Can I smelt silver at home?
- Can I melt silver and gold together?
- How can I reduce the power consumption of my induction furnace?
- How do you melt gold dust?
- How hot can induction heating get?
- What are the advantages of electric heating over other types of heating?
Why do you need an induction melting furnace?
Induction furnaces continue to drive the market in the foundry industry, therefore, you need a gold melting machine for the following reasons:
Increased efficiency- The efficiency of a gold melting machine closely relates to its power requirements. The high voltage primary coil in the gold melting machine allows the furnace to heat up quickly providing higher thermal efficiency for all round melting.
Reduced cost of operation- The financial implication of running your gold melting machine goes hand in hand with energy efficiency. The use of a jewelry furnace reduces power consumption, therefore, saving production cost.
Improved metallurgical function- The principle behind induction melting revolves around the use of high voltage primary coil to generate an electromagnetic current that heats the metal. The induction furnace performs a function called ‘electromagnetic stirring’ which causes molten metal to become even or uniform for casting.
Reduced oxidation losses- The gold melting machine reduces oxidation loss.
Cleaner melting operations- The gold melting machine has a less negative impact on the environment compared to electrical furnaces. This jewelry furnace reduces the emissions of gas, smoke and dust associated with other types of furnaces.
How does an induction melting furnace work?
Induction melting furnaces operate on a radically different principle to the cupola version. The induction furnace uses coil heating elements embedded within a crucible or integrated into the walls of the heating chamber itself and produces a magnetic field. These convert electrical energy into heat which is radiated through the material with an outstanding degree of thermal uniformity. The magnetic field can change directions depending on the direction of the current flow. An alternating current that passes through the coil causes a magnetic field that changes in the same direction at the same speed as the current. For instance, a magnetic field switches directions 60 times a second if the current is 60Hz AC.
How to melt different kinds of metals?
Metal melts at different temperatures and may require certain types of melting furnaces. Metal melting requires a lot of heat. Melting furnaces commonly used in melting metals are; induction, cupola, electric arc furnaces, etc.
The induction furnace melts metals by holding the charge in a nonconductive crucible. The crucible is surrounded by a coil of copper wire that transfers heat to the crucible.
How to choose the induction melting furnace you need?
Choosing the best jewelry melting furnace for your needs require the following considerations:
Know the melting points of the metals you will be melting because induction furnaces are meant to heat to a specific limit. You have to know if the heat will be enough to melt your metal.
The melting capacity of the gold melting machine, that is the size.
The energy need of the gold melting machine should also be considered.
The gold melting machine price which will be determined by the size, model and purpose of the furnace.
The furnace crucible will also determine the type of gold melting machine.
The method of molten metal removal of the furnace. This is usually determined by the design of the gold melting machine which could be tilted for metal removal or removable with tongs.
How efficient is induction heating?
The induction heating is an efficient process of melting metals. Induction heating has a minimal wasted energy with direct transfer of energy to the part being heated. This high efficiency results in significant power savings. Induction heating proves to be a highly efficient method for industrial heating applications.
Compared to torch and oven heating, induction heating has a number of advantages, such as; induction transfers more power to the load, no ramp up, does not heat up a working environment that may lead to energy wastage.
Induction heating is also efficient because it delivers power only where it is needed.
What temperature can the induction melting furnace reach?
Induction furnaces do not have a limit to the temperature that they can melt. The gold melting machine temperature can be as high as 3000 degree celsius. Therefore making it suitable for precious metal melting. For platinum group melting, the required heating temperature is usually 2000 degree celsius.
What can I use as a crucible?
Crucibles for metal melting generally have a higher melting temperature compared to the material being melted. Crucibles for melting metal in a jewelry furnace are graphite crucibles, silicon carbide crucible, quartz crucible, etc.
When melting below 1600 degree celsius, a graphite crucible is recommended. When melting metal above 1600 degree celsius, a quartz crucible is recommended.
What is the difference between an electric arc furnace and induction furnace?
Electric arc furnace works on a principle of generating heat by arc to melt metals while in an induction arc furnace, it is achieved using electromagnetic induction.
The induction furnace is heated faster and has a higher thermal efficiency. The heat in this furnace is generated inside the furnace so that heating speed is high. In an electric arc furnace, the heat of the arc after the material is cleared must be transferred to the molten metal through the slag which is indirect heating. Thermal efficiency is poor as heat of arc is lost through furnace cover and wall.
In a gold melting machine, the temperature of molten metal is relatively uniform due to electromagnetic stirring which is uneven in an electric arc furnace.
What is the difference between smelting and melting?
Melting and smelting are similar terms used to convert a solid material into liquid especially in metallurgy. Melting simply means the process of converting the entire solid material into liquid when heating in a gold melting machine. Melting is also called fusion. During melting, the internal energy of the substance increases by heating.
Smelting on the other hand is not only the conversion of solid material into liquid state but also removes metal from its ore in its purest form. An ore is a naturally occurring solid mineral from which a metal or valuable mineral can be extracted. The smelting process has two requirements; heat treatment and reducing agents.
How do you smelt gold with borax?
Borax plays an important role during the gold refining process. Borax is placed along with gold ore in a crucible and then heated. The heating action is what triggers the borax to work. The borax is responsible for separating the gold from its ore and purifying the metal. As all material melt down, they separate from one another. As the process continues, the borax causes the other minerals to oxidize and break down even further. Gold is unaffected by this reaction, it sinks to the bottom of the crucible intact.
Due to the affordability of borax and effectiveness at extracting gold, borax-based refining technique was popular during the 19th century gold rush. It still continues today among individual prospectors and different scales of mining operations.
How do you separate gold from other metals by melting?
Gold can be separated when mixed with other metals. The process involves the following:
Heat the furnace to a temperature reaching 1200 degree celsius.
Mix the silica and sodium borate chemicals into the furnace to create the slag.
Wait for the metals to dissolve, it takes some time for the metals to dissolve and the slag to develop.
After the slag has been heated for long enough, the molten gold begins to dissolve away. Allow the gold to slip down into the smelting vessel. After this has occurred, allow the gold to cool, remove from the smelting vessel and remove the slag.
How do you melt gold jewelry?
Unwanted gold can be melted and used to make other types of jewelries. Gold jewelry can be melted using the following methods: propane torch, gold melting machine, resistance furnace or a 1200 watt microwave oven.
Of all the methods of melting gold jewelry, the gold melting machine method is highly recommended. The gold melting machine is highly efficient for both small and large size gold production. This method is also efficient because the heating system is produced from the alternating magnetic current and directed into the crucible, hence no energy is lost.
Simply heat up the furnace and charge your gold jewelry, wait for some minutes and your gold jewelry is already melted. Remove molten gold from crucible.
How do you get gold from gold ore?
A process of separating gold from its ore is referred to as “cupellation”. This process involves treating ores under high temperatures to separate noble metals such as gold and silver from base metals. Base metals such as copper, zinc and lead will oxidize whereas noble metals will not oxidize. Cupellation involves melting gold ore at temperatures in excess of 960 degree celsius, at this temperature, the base metals oxidize while the gold remains on top of the solution. In other words, gold is extracted from its ore and heated in an induction furnace at 1064 degree celsius, in order to elevate the gold above its melting point.
How do you get impurities out of gold?
Many impurities are burned off in the furnace, other metals remain. Gold ore extracted from mines in the earth contains a significant amount of impurities, including traces of other metals. In order to separate the gold from other metals, chemicals such as cyanide solution or mercury are introduced to the gold. This process causes the gold to coagulate, and form nuggets and clumps of gold.
Another process of removing impurities out of gold is to place the gold ore in a crucible. Put the crucible in a gold melting machine. Heat to 1,100 degrees Celsius. Dross will rise to the surface. Periodically remove the crucible from the furnace and skim the impurities off the surface of the molten gold. Stir the gold after each removal of dross and before returning it to the furnace. Repeat this process until dross stops rising to the surface.
How can I reduce the power consumption of my induction furnace?
There are some practices that help to reduce power consumption of a gold melting machine. These practices include;
Faster charging speed- charging should be done rapidly and metal should be put into the furnace as fast as the furnace is able to melt it under full power. A faster automatic charging system can reduce energy consumption.
Avoid overfilling- Overfilling the furnace, that is, having cold charge materials lying above the upper melt line level recommended by the furnace manufacturer will cause wasted energy. The problem is twofold. First, this will cause overheating of the jewelry melting furnace components in the top part of the furnace leading to energy loss. Second, with the furnace overfilled, the lid cannot be closed.
Use clean scrap- Dirty charge material wastes a lot of energy and increases electrical consumption.
Remove slag more quickly- It is also important to reduce the time needed to remove slag during the melt cycle.
Save power with maintenance- Close attention to normal maintenance procedures can produce surprising energy savings at minimal additional cost.
Keep a lid on- The best way to reduce heat loss through radiation is by keeping the lid on. This means closing the jewelry melting furnace lid very quickly after adding charge material and after taking temperatures or adding alloying materials.
What is the difference between an electric arc furnace and induction furnace?
Electric arc furnace uses its arc to generate heat to melt metals, while the induction furnace uses electromagnetic induction to generate heat to melt metals.
In the electric arc furnace, the heat of the arc after the material is cleared must be transferred to the molten metal through the slag, which is indirect heating. Thermal efficiency is poor. The furnace is in the shape of a basin, and plenty of the heat of the arc is lost through the furnace cover and the furnace wall. While the induction furnace is heated faster and has higher thermal efficiency. The heat is generated in the furnace, so the heating speed is high.
The oxidative burning loss of elements in an induction furnace is less. Because there is no ultra-high temperature of the arc in the induction furnace.
Does induction use less electricity?
One of the advantages of the gold melting machine is its use of less electricity compared to other types of furnaces. The heat generated by the furnace is used within the jewelry melting furnace, no heat escapes to cause extra electricity charges. The jewelry melting furnace is highly energy efficient and can help you save up to 50% of energy used in smelting and melting metals. The jewelry melting furnace is integrated with a power supply capable of producing heat with lower rates of heat loss. For instance, a gold melting machine can melt metal of up to 1450 degree celsius using less than 600kWh of electricity.
At what heat (temperature) does gold melt?
Gold melts at 1064 degree celsius. The boiling point of gold occurs at 2845 degree celsius. Pure gold melts at 1064 degree celsius but if other alloys are present (copper is the most commonly used base metal), then the temperature required to melt gold will vary. Due to the softness of pure gold (24 karat), it is usually alloyed with base metals for use in jewelry thereby, altering its ductility, melting point, colour and other properties. Alloys with lower karat ratings, for instance 22k, 18k, 14k or 10k contain higher percentages of copper or other base metals or silver or palladium in their alloys.
The melting of gold is not the only method to regain raw material for the production of new jewelry, coin, industrial or dental gold. Another method of determining the degree of purity and quality of gold is through the XRF analysis method.
What flux do you use to smelt gold?
The following types of fluxes can be used to smelt gold: Borax, silica, hydrochloric acid, ammonium chloride, sodium nitrate, sodium carbonate, zinc chloride etc.
The use of flux for gold smelting has its benefits which includes; lower energy cost, higher profit margin, removal of mercury that can be harmful to health, and a pure separation process.
How much borax is required to melt gold?
Borax allows you to melt your gold in a pure and harmless manner. The quantity of borax for melting in a gold melting machine will be determined by the quantity of gold to be melted. With some borax and heat, it is possible to extract gold from a simple ore. Once the borax melts, it lowers the melting temperature of everything in the ore.
Generally when melting gold, a small amount of borax is needed for melting. Traditionally, for gold melting, flux mixture should contain 40 to 50% of borax, 10 to 15% of soda ash and 1 to 5% of silica.
What is the process of smelting gold?
Smelting gold is accomplished by using high pressure, heat and various chemicals to break down the ore and melt the gold to separate it from impurities. To extract gold from its ore, the temperature must be at1046 degree celsius.
The process of smelting gold is performed in less than two hours to ensure complete separation of impurities from precious metal.
The first step in the process of smelting gold is the preparation of flux. The most common forms of flux used in gold smelting are borax, sodium nitrate, and silica. The percentage of these fluxes varies and it depends on the composition of the precipitate. These fluxes are necessary to bring impurities to the surface.
When the mixture of the flux and gold are placed in a gold melting machine, both materials melt in the furnace. The jewelry furnace is heated to high temperatures exceeding 900 degree celsius. After the mixture melts, the precious metal and impurities separate. This is the aim of the entire procedure. Gold is denser than most impurities in it. This allows the gold to settle down.
In the smelting process, the most important aspect is separating the impurities and flux from gold. Gold settles at the base of the crucible after melting, this makes it easy to drain the impurities that have risen to the top. This leaves the gold at the bottom of the furnace crucible that can be poured into a mold.
Can you smelt gold in cast iron?
A cast iron can be used for smelting gold but it is recommended to use a graphite crucible for smelting. Using a cast iron will result in loss of precious metal, contamination of precious metal and a slower smelting process. For an effective smelting process, a cast iron cannot fit into a jewelry crucible rather an open stove or kiln, which can’t really get to the temperature you need to smelt gold. Smelting in a cast iron will not remove any impurities.
Using a cast iron for smelting can cause the cast iron itself to reach its melting point before completing the gold smelting process. Therefore, we recommend you use a graphite crucible for smelting gold.
Can I smelt silver at home?
Silver is one of the most common precious metals used in jewelry, electronics and medical supplies. It is not only mined and smelted on an industrial scale, it can also be smelted at home.
To smelt your gold at home, you need access to a high temperature gold and silver smelting equipment. Determine the size of silver you want to smelt. This will tell the size of the smelting equipment you need. Although most “do it yourself” smelting requires a mini sized furnace.
You can remove the most common metal in silver ore using elements that bond with oxygen at lower temperatures than silver. This oxidation process will make copper oxide, zinc oxide and lead oxide to float on top of the crucible allowing the slag to be removed.
Sodium nitrate, silica and sulphuric acid cause this reaction.
Load the solid silver ore into your crucible and set in the smelting equipment. Silver melts at 962 degree celsius. Heat up the smelting equipment and allow the silver to melt. When the mixture becomes liquid, impurities from the silver ore rises to the surface and can be skimmed off to leave pure silver behind.
Can I melt silver and gold together?
Yes, you can melt gold and silver together and the resulting metal is referred to as “electrum”.
Gold melts at a temperature of 1064 degree celsius while silver melts at 961.8 degree celsius. To alloy these two metals, melt the gold to hot liquid, add the silver metal. This will dissolve immediately in the blazen liquid gold.
The heating process is what does the alloying so trying to stir up the liquid metal will not help or quicken the alloying of the two. The heat needs to stay as concentrated as possible.
Once the flames turn from bright orange to a bright yellow, this confirms that your metal is thoroughly atomically combined which is important to assure a well-rounded metal alloy. If the metals are not well blended, they may be problematic at the production phase.
Alloying gold with silver is beneficial as it makes both metals hardy in endurance and more flexible in construction. The bright and light color shades are also quite beautiful to look at and adorn.
How can I reduce the power consumption of my induction furnace?
Here are the major ways in which you can reduce the power consumption of a smelting equipment to reduce energy cost without sacrificing productivity.
Maximize the use of your smelting equipment- One of the best ways one can reduce how much energy their smelting equipment uses is by using the equipment more effectively. Short holding times can improve the efficiency of your smelting equipment, because longer holding time requires more energy consumption.
Make any necessary changes to your operating procedures- Another great way to reduce your smelting equipment energy consumption is by replacing your current melting equipment. Ensure you give your foundry a thorough investigation to determine some of the best operational changes that you can make to cut down on energy use.
Boost your charging speed- Apart from long holding times, charging speed can also have a major impact on the use of your smelting equipment. Long charging times caused by manual or magnetic crane charging can lead to more energy use. You want your charging to be done rapidly and efficiently, use automatic charging systems.
Streamline your temperature measurement- When you check the temperature of the smelting equipment regularly, you are losing valuable time and wasting needed energy. By using a computerized temperature control system, you can reduce the need to check furnace temperature.
How do you melt gold dust?
Different methods can be used to melt gold dust; gas torch, gas furnace, electric furnace, coal furnace. Gold dust can be wasted when melted with a gas torch.
Here is how to melt gold dust using a induction furnace:
Add a very little amount of borax into the furnace before placing your gold dust.
You can go ahead to add some flux, flux is a mixture of borax and sodium carbonate. You can mix it with gold dust before melting or during melting.
Go ahead and melt the content of the crucible.
How hot can induction heating get?
Induction heating can be as low as 100 degree celsius and as high as 3000 degree celsius. The temperature of a gold smelting equipment with a graphite crucible can reach 1600 degree celsius suitable for melting gold, silver, stainless steel and copper. Higher melting metals such as platinum group metals whose melting temperature can reach 2000 degree celsius can be melted easily with an induction heat.
What are the advantages of electric heating over other types of heating?
The electric heating has advantages that makes it a smelting equipment of choice over other types of furnaces. The advantages of an electric heating system include:
Uniform stirring of charge that gives a homogenous molten metal composition.
The electric heating furnace helps to save between 15% to 30% of energy.
The heating temperature can be easily monitored without having to open up the furnace constantly.
The speed of melting is fast, therefore, saving production time.
The electric smelting equipment does not make noise or release harmful gases into the environment.
It helps to achieve clean melting operations.
The water cooling unit enables the electric smelting equipment to melt continuously for long hours.
Easy to charge, pour and control, hence, it is easy to operate.